Michael Dickey
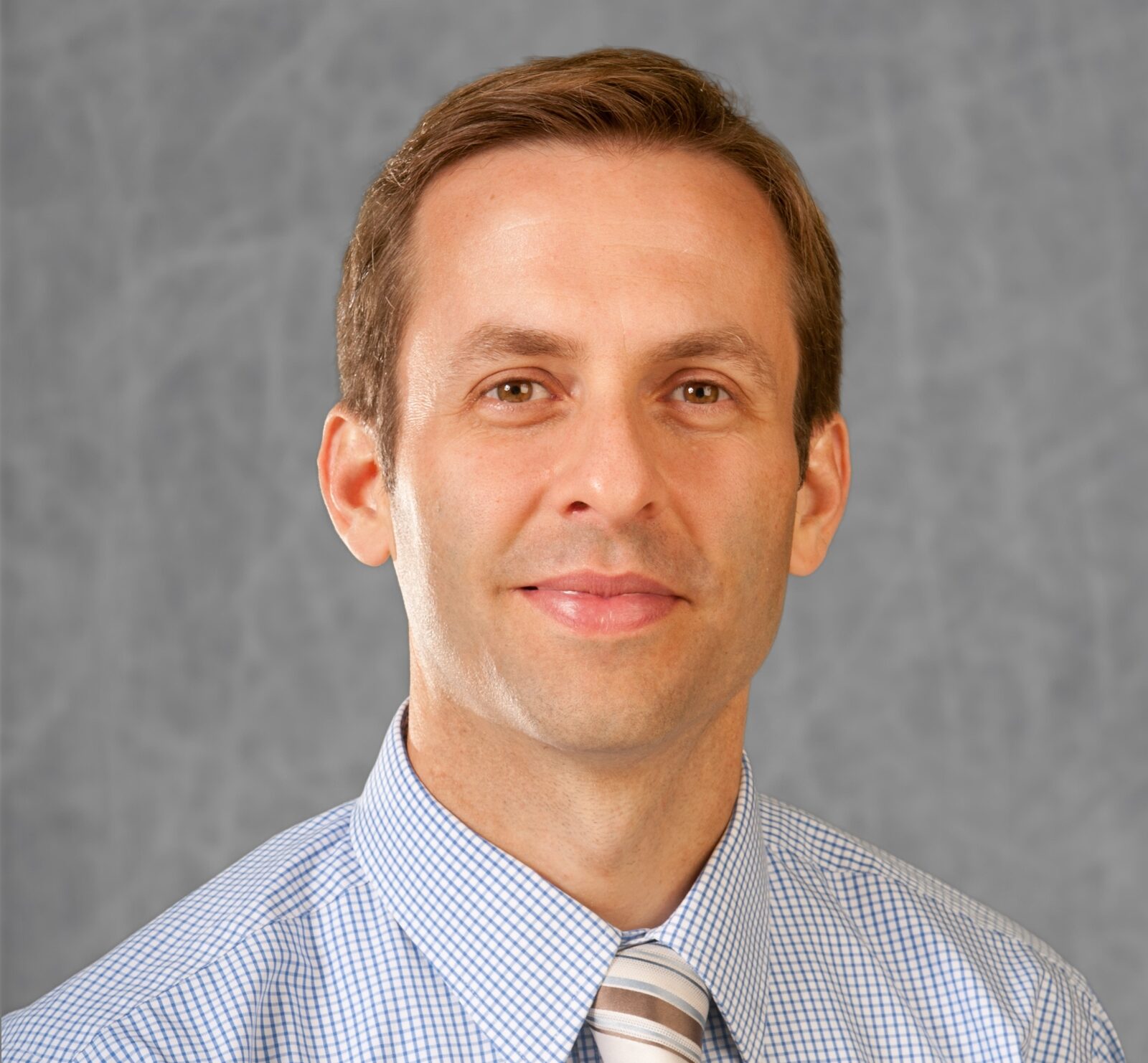
Bio
The Dickey group is studying new ways to pattern, actuate, and control soft materials (gels, polymers, liquid metals). A common theme of our projects is the importance of thin films, interfacial phenomena, and microfabrication. One interesting application of our work is for “blue energy”; that is, harvesting energy from the motion of waves and water for clean energy sources.
SHORT DESCRIPTION OF INTERESTS:
Harvesting energy from the environment.
https://www.cbe.ncsu.edu/dickeygroup/
Publications
- Connecting the Dots: Sintering of Liquid Metal Particles for Soft and Stretchable Conductors , CHEMICAL REVIEWS (2025)
- Multicomponent shape-memory microfibers electrospun with precisely tunable thermal triggers , COLLOIDS AND SURFACES A-PHYSICOCHEMICAL AND ENGINEERING ASPECTS (2025)
- Regenerable liquid metal nanozymes enable pH-regulated multi-enzyme mimicking , MATTER (2025)
- Roadmap on embodying mechano-intelligence and computing in functional materials and structures , SMART MATERIALS AND STRUCTURES (2025)
- Ultrarobust and Lightweight Electro-Pneumatic Actuators for Soft Robotics , IEEE TRANSACTIONS ON ROBOTICS (2025)
- pH-Switchable Multi-Enzyme-Mimicking via Liquid Metal Nanozyme , SMALL (2025)
- 3D-Printing of Hierarchical Porous Copper-Based Metal–Organic-Framework Structures for Efficient Fixed-Bed Catalysts , Chem & Bio Engineering (2024)
- 4D printing roadmap , Smart Materials and Structures (2024)
- A Guide to Printed Stretchable Conductors , CHEMICAL REVIEWS (2024)
- A highly conductive and ultra-stretchable polyaniline/cellulose nanocrystal/polyacrylamide hydrogel with hydrophobic associations for wearable strain sensors , JOURNAL OF MATERIALS CHEMISTRY A (2024)
Grants
The proposed research aims to develop a fundamental understanding and control of organic vapor deposition on flat and porous surfaces. Specifically, it targets depositing low surface energy coatings on polymer films and nonwovens using a novel process technique called molecular layer deposition (MLD).
We propose to acquire the LPKF ProtoLaser R4, a class 1, pico-second laser specially designed for cutting, fabricating, and patterning a wide range of materials that will be of critical use for advanced manufacturing. Features as small as 20 microns can be easily developed using this machine and it can be used to directly process a wide range of materials for energy, biomedical systems, soft materials, inorganics, and electronics applications.
Lower limb amputees rely on prosthetic sockets as the interface with their prosthetic legs. The prosthetic sockets only work well if they fit residual limbs of amputees perfectly. Unfitted sockets cause various health issues for lower limb amputees and could significantly limit amputees������������������ functionality. Currently, prosthetists lack the capability to diagnose socket fit during the socket fitting procedure, which limits their capability to customize the sockets for better fit. The proposed Enable system will be used as a diagnosis tool for prosthetists. Based on a novel material, which changes color based on loaded pressure, this Enable system will permit prosthetists to evaluate the socket fit by observing the pressure distribution on the residual limb directly. During the proposed project, we will develop the smart liner system and test it through both bench tests and human subject tests. We will also validate that prosthetists will be able to use the smart liner to make appropriate socket fit diagnosis through simulated clinical cases.
The goal of this proposal is to collaborate with ASU to study new types of liquid metal pastes.
We propose to study and enable ���������������reverse electrowetting������������������ as a means of energy harvesting. The appeal of the proposed technique is that it is a platform built from soft materials (elastomers, fluids) and converts mechanical energy directly into electrical energy using a small footprint. The project is based on exciting preliminary results obtained by a summer student in our laboratory. Classic ���������������electrowetting on dielectric������������������ utilizes electrical energy (voltage, current) to induce a droplet to wet a surface (mechanical work). It typically consists of a drop of liquid (e.g., water, ionic liquid, etc.) resting on a thin, non-wetting, electrically insulating substrate supported by an underlying electrode (Figure 1, left). In the absence of potential, the droplet assumes a round, non-wetting shape due to surface tension. The application of a potential between the drop and the underlying electrode causes the droplet to spread across the substrate to maximize capacitance. The final shape of the drop represents a balance of the forces of surface tension and capacitance.
The goal of this project is to develop a class of sensors based entirely on soft materials including hydrogels, elastomers, and liquid metals. The appeal of this approach to sensing is that (1) the hydrogels are biocompatible and in principles can be interfaced with the skin, and (2) the materials are all soft and therefore can conform to the skin in a comfortable manner. The premise of the sensing arises from doping the gels with responsive molecules that can induce a detectable signal that can be integrated with other components being researched within the ASSIST program.
This projects focuses on efforts towards commercialization of a flexible thermoelectric module manufacturing process developed with prior funding from National Science Foundation through Advanced Self-Powered Sensors and Integrated Technologies (ASSIST) Engineering Research Center. These modules can harvest body heat and the generated electricity can be used to power wearable electronics providing the ability to perform long-term continuous sensing. A process compatible with roll-to-roll manufacturing is described. The proposal addresses potential failure mechanisms that may have an impact on the long-term reliability of the modules.
This proposal focuses on a way to self-power devices by converting mechanical energy into electricity. The approach will use all soft materials and can convert electricity via all modes of deformation.
Thermal control in engineered systems is typically accomplished using fixed heat flow paths and by varying the amount of heat (energy flow) provided in order to control temperature at specified point(s) within the system. The goal of this work is to develop a practical device that allows heat flow paths to be adjusted dynamically via more advanced thermal control logic and tuned thermal interfaces.
The goal of this proposal is to study liquid metals as next generation thermal interface materials.